

This is frequently the case in double tees, which form the driving surfaces in parking structures. Pretension prestressing can impart camber to the member that is useful in resisting service loads. The piece can then be stripped from the form and moved to storage. When it hardens to its specified strength, the strand is released and axial compression is transmitted to the cross-section of the member. As it cures, the concrete bonds to the strand. The amount of tension applied can range from a few thousand to tens of thousands of psi depending on design.Īfter tension has been applied to the strand, concrete is poured into the form. The strand is anchored and then pulled until it reaches a desired tension. To prestress a concrete member, a high-strength steel strand is laid in the form before concrete is placed. Prestressed concrete may be precast or cast in place, in this article we have focused on precast. This is most common in long span beams found on bridges and railway viaducts, slab, and concrete piles. The main purpose of having prestressed concrete is to increase the load that the member can withstand. The steel cables reacting to the release, transfers the tensile stresses into the concrete, rendering an even stronger structural component.
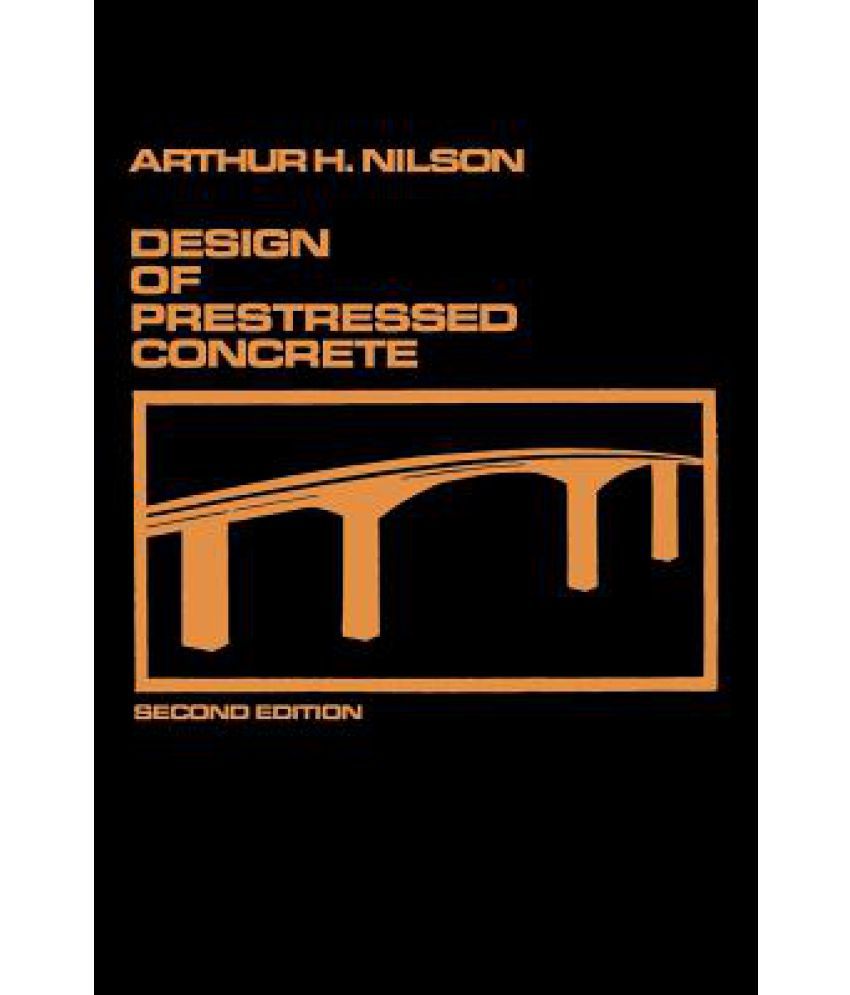
Once the concrete cures to its required strength, the tensioning is released. These cables are tensioned (stretched) to approximately three-quarters of their ultimate strength. Prestressed concrete is achieved by casting concrete into pre-assembled forms in combination with rebar and steel cable (strand) reinforcement. It is also known as pre tensile concrete, and is made by applying tension to the steel rebar during the curing process. Prestressed concrete is substantially “prestressed” (compressed) during production, in a manner that strengthens it against tensile forces which will exist when in service.
